Spatterings, pits, defects in weld beads – these are the thorns in the sides of many a newly minted accelerator cavity, marring their interior walls and getting in the way of healthy accelerating gradients.
Scientists at Fermilab are testing a new method of removing these blemishes from superconducting radiofrequency cavities. It’s called centrifugal barrel polishing, and the team hopes it will yield a consistently reproducible mirror-like finish, and so consistent cavity performance.
“What we’re doing is similar to the process of polishing gemstones,” said Fermilab’s SRF Materials Group Leader Lance Cooley. “We’re making shiny jewels.”
Of course, with niobium cavities, the purpose is not to turn the cavity’s inner wall into shimmering eye candy. The fewer surface imperfections inside the cavity, the more easily a particle beam will accelerate from one end of the cavity to the other.
Charlie Cooper proposed the method – known more familiarly as tumbling – as a potential cavity-polishing method at Fermilab. He has been testing various fine-polishing procedures over the last year. Approaching cavity-polishing from a metallographic standpoint, he set out to develop a process that would be environmentally friendly, safe and repeatable.
His efforts extend past procedures tested by DESY’s Waldemar Singer and KEK’s Kenji Saito, who tested mechanical polishing that would remove 120 to 150 micrometres’ thickness from the cavity wall. They laid the R&D foundation for mechanical bulk removal of metal, which shaves off cavities’ deep pits and other defects.
Cooper’s team added further fine-polishing steps that, so far, result in a finish smoother than those obtained after the final electropolishing steps of the ILC baseline procedure. The final tumbling step, which utilises a colloidal silica, is key to the mirror-like finishes currently obtainable. Early results show that tumbling can bring cavities to an average roughness on the scale of mere tens of nanometres (the average height of the various bumps and craters over a specified area of the metal). Very preliminary tests also show that tumbling can help cavities achieve gradients that would satisfy the ILC baseline requirements.
The active ingredients in tumbling are abrasive polishing materials, called medias. Themselves jewel-like in their myriad colors, their various densities and shapes are appropriated for different degrees of mechanical polishing.
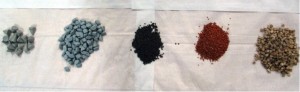
Medias are tumbled inside the niobium cavities. The grey cones (far left) are a plastic with aluminum silicate, used for bulk removal. The powder blue media (second from left) are ceramic abrasives, useful as a first-pass media. A hardwood cut into small cubes (far right) is also a useful abrasive.
The medias fill half the cavity’s volume. The cavity is placed horizontally into the barrel of a tumbling machine, which can hold up to four nine-cell cavities. The barrels revolve around a central shaft 115 times every minute. Individual barrels simultaneously rotate at the same speed around their own axes, turning in the direction opposite the main shaft’s rotation.
As the cavities spin, the medias inside them slide against the inside wall to remove material. The types of medias, their sizes and their force against the wall determine the removal rate.
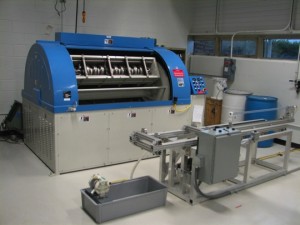
The tumbling machine (left) can hold two nine-cell accelerating cavities, rotating them up to 115 turns per minute. The rinsing device (right) washes the media out. Cavities must be absolutely free of any extraneous material after tumbling.
“It’s like sanding a piece of wood,” Cooper said. “You’re putting abrasive material inside the cavity, but you’re doing it in a three-dimensional geometry.”
So far Cooper’s team has tumbled 1.3-gigahertz single-cell and nine-cell cavities as well as 3.9-GHz single-cell cavities. Their goal is to consistently polish the cavities to acceptable accelerating gradients.
In one test, they subjected a nine-cell cavity with a 200-micrometre pit to intermediate-level tumbling, scouring out the defect and so bringing the accelerating gradient from 19 megavolts per metre to 35 MV/m and a quality factor above 1010.
Another result came from a virgin single-cell 1.3-GHz cavity. After an intermediate-level tumbling polish, the cavity achieved just more than 40 MV/m. Nearly up to that gradient value, the cavity maintained a quality factor just above 1010.
Though the results come very early in the rigorous testing process, they are motivating. The team is working towards the goal of replacing the more elaborate, acid-intensive and costly electropolishing steps of the current ILC baseline. So far, a final, very mild electropolishing has been applied to tumbled cavities as a precaution, but they hope that this too could be simplified or removed.
They are currently cold-testing cavities to see the effects of the mirror-like finish on accelerating gradient and quality factor. The results will help to further tune the tumbling process.
Though tumble finishing is a common practice in industry – tumbling is used for refinishing auto parts, for example – those practices are typically meant to polish the outsides of things, not the insides. For that reason, among others, Cooper had to develop a different approach to tumbling rather than adopt industry wisdom.
“I obtained many different medias and tried many different recipes – I did a lot of cooking,” Cooper said.
Scientists will apply tests of tumbling to cavities at different stages in the polishing process. In the future, they also hope to extend tests to various rinsing methods and to cavities of a shape or frequency different from the ILC-type cavities.
“I’m surprised that in a few months Charlie has taken some rocks and created a pretty nice system for polishing cavities,” said Cooley.
Recent Comments