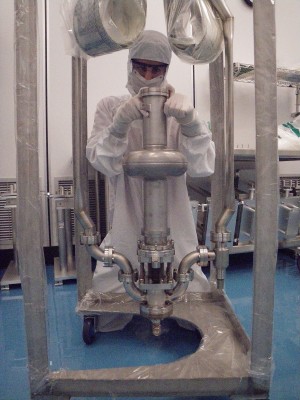
Sam Posen assembles a Nb3Sn cavity to a test stand in the clean room. Image: Cornell Laboratory for Accelerator-based Sciences and Education (CLASSE)
Accelerator physicists are driven by one goal: to make particles go at high energies and in perfect beams at the highest efficiency and lowest cost possible. There are many different accelerator technology options for all sorts of particles, different types of colliders, storage rings and linacs, and different goals: medicine, light source, and, of course, fundamental research.
A big player in the development of superconducting radio frequency technology, the technology for the ILC, has always been Cornell University in Ithaca in the United States. It is here that Maury Tigner developed the concept for the linear collider in 1965, and some of the standard SCRF textbooks were written by Cornell’s Hasan Padamsee, who has since become head of Fermilab’s Technical Division. Now Cornell is working on a technology that could make superconducting cavities even more efficient: niobium alloyed with tin.
Niobium-three-tin, or Nb3Sn, holds great potential for all uses of SCRF because of its low surface resistance at a relatively high temperature and potential to operate at very high fields. With low surface resistance at 4.2 Kelvin (conventional all-niobium cavities typically operate at 2 K) less power is needed for the cryoplants that cool the accelerator – a factor that could greatly reduce costs. And high fields equal high accelerating gradients which, once the technology has proven its principle, would equal fewer cavities, a shorter accelerator and thus also less money.
Niobium cavities are well understood and are in use in many places around the world while R&D into improving and inspecting them goes on, for example at KEK, DESY or Fermilab. Different materials and coatings have always been part of that R&D, and Cornell isn’t the first lab to pick up the idea of coating niobium single-cell cavities with Nb3Sn. However, Cornell has recently made important progress with the material, achieving for the first time very small surface resistance in Nb3Sn-accelerator cavities at usable gradients.
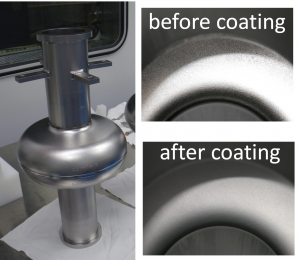
Cavity before and after coating. Image: Cornell Laboratory for Accelerator-based Sciences and Education (CLASSE)
The Nb3Sn programme at Cornell is a very small team – essentially Cornell physicist Matthias Liepe and graduate student Sam Posen. Sam, who started in 2009 and is about to hand in his thesis, commissioned and calibrated the lab’s own coating furnace and is in charge of all Nb3Sn tests. Single-cell cavities enter a chamber inside an ultra-high-vacuum oven – the coating furnace – all shiny and sparkling and come out all dull and lacklustre – but only to the eye, not to the accelerated particles. In the 1100-degree furnace tin vaporises and diffuses onto the surface of the cavity, forming an alloy in extremely controlled ratios. “We know because of temperature-mapping tests that the surface is very uniform,” explains Sam Posen, “so they show very uniform performances.
The coated cavities reached gradients of approximately 14 Megavolts per metre with a quality factor at a temperature of 4.2 K of 2 x 1010; 20 times the quality factor Q of standard niobium cavities, for which the Q at the same temperature is 6 x 108. So far, three single-cell cavities that have been produced using the coating furnace have reached these gradients. The next challenge: he currently has a cavity on his desk that has been electropolished instead of undergoing buffered chemical polishing (BCP). “It’s exciting to use such a recently accepted technology on a material that it has never been applied to.”
There is currently no project attached to the Nb3Sn research, though its outcome could be transformational for many future accelerators and even (upgrades of) the ILC. “This is really fundamental research in accelerator physics,” says Sam. “But it’s exciting to know that the application of my work might benefit many accelerator-driven sciences, and even industry.”
Recent Comments