The Global Design Effort (GDE) was created by the International Committee for Future Accelerators with the specific mandate to develop a design for the ILC based on superconducting radiofrequency acceleration. One of the earliest goals of the GDE was to pursue an aggressive R&D programme to develop high-gradient cavities. We set an ambitious goal of 35 MV/m, and in 2010 we achieved the major milestone of producing 35-MV/m cavities with 50 percent yield. Now, our goal has shifted towards refining the process of reliably producing high-gradient cavities, as well as working toward developing a cost-effective industrial capability worldwide.
Last year, GDE Project Managers Marc Ross, Nick Walker and Akira Yamamoto visited industries around the world in order to familiarise potential vendors with the detailed technical issues that are involved in producing high-gradient superconducting cavities. Those visits were quite useful in aiding technology transfer to industry and informing us better about the capabilities and issues for industrial vendors.
We have recently begun a second round of industrial visits that are aimed at facilitating the development of cost-effective mass production of cavities and cryomodules for the ILC. The primary cost driver for the ILC is production of roughly 2,000 operational high-gradient cryomodules. Making this process cost-effective is one of the most important objectives of the GDE as it prepares to produce the Technical Design Report. The scheme we develop will guide future R&D and be the basis of the costs included in the TDR.
The GDE project managers, led by Akira Yamamoto, have developed an informative report to accompany their industrial visits. In it they list several key themes that need to be developed in order to prepare for industrialisation and for making a reliable cost estimate:
- Cavity and cryomodule gradient specification and projected production yield (laboratory’s responsibility)
- Flexible technical specification based on a ‘plug-compatibility’ concept with interface definition and specifications (as requirements for manufacturers)
- Production process and industrialisation models
- Models for international cooperation, including in-kind contributions from nations and/or laboratories
A central goal of our R&D programme has been focused on the first theme, and we have recently had good success at achieving high gradient. We will now work towards refining the processes involved in order to obtain, we hope, a yield approaching 90 percent during the next phase of the TDR preparations. In addition, we have also developed the plug-compatibility concept (see second point above) to enable each contributing institution to optimise their process for delivering subsystems. This concept is being tested in a real-life situation for the S1-Global tests at KEK. We are now increasing the efforts specified in the last two bullet points, which will be essential for worldwide production of the SCRF main linac cryomodules components. Lastly, we must strive to develop plans for production that will be very cost-effective.
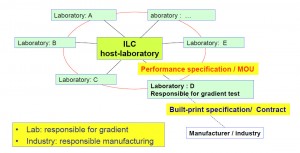
A schematic view of production, such that industry assumes responsibility for manufacturing and the ILC laboratories assume responsibility for performance.
The ILC Project Advisory Committee emphasised this last point in their technical review last autumn. They suggested that we look at developing a model for mass production similar to what was done for the LHC magnets. In that case, as much performance risk as possible was assumed by the laboratory; industry was relied upon to produce the components to specifications. Although this scheme requires far more from the laboratory in terms of integrating the components and taking responsibility for performance, it enables industry to do what it does best within minimum risk, and that is to build components to well-defined specifications. We believe this approach will considerably reduce costs from the present level where industry is assuming more performance responsibility. For that reason, we are extending the dialogue with industry to better understand how they would like to approach mass-producing SCRF cryomodules.
It may seem early to work on optimising the production process, but it will take a concerted effort and time to develop a reliable and cost-effective scheme for constructing the SCRF main linac. We believe the present scheme, which is to develop our plan in close collaboration with industry, will help us accomplish this goal. It will therefore also better enable us to be able to reliably estimate the cost of the main linac for the ILC Technical Design Report.
Recent Comments