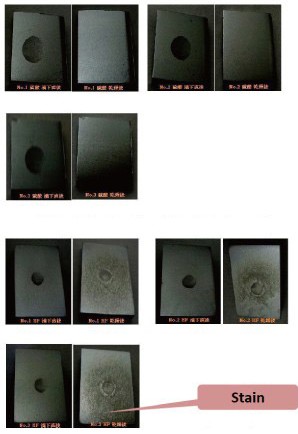
Comparison of stain forming with sulfuric acid solution (top) and hydrofluoric acid solution (bottom). Image: Motoaki Sawabe
Worrying about blemishes on the skin is not just an issue for people who pursue personal physical beauty, but also for accelerator scientists. Scientists and engineers at KEK have found a way to deal with unwanted stains on the inner surface of superconducting cavities, which might be one of the causes of performance limitation.
Since the development of the Kyoto camera, a high-resolution camera that enables the optical inspection of the inner surface of niobium superconducting cavities, scientists have noticed that brownish stains exist on the cavity walls. When they were vertically tested to evaluate their performance, the stains were sometimes found around the spots where heating is observed.
The inner surface of the superconducting cavities is polished to a mirror-like finish, since any defects of debris inside of cavity will interfere with its performance.
Fabricated cavities are at first coarsely electropolished, then annealed. This is followed by inspection and tuning. It is then given another electropolish finish for micro-level smoothness. Scientists suspected the brown spots probably formed at some point during this procedure.
To understand what they are, Motoaki Sawabe and his colleagues at KEK’s STF surface research group decided to reproduce the stain. First, they dripped two microlitres of electropolishing solution on the chemically polished niobium plates. The plates were left for an hour, rinsed with pure water and dried at 50 degrees Celsius. They were able to reproduce the stain, but not every time.
Then they tried the same procedure with two different solutions: one containing sulfuric acid and another with hydrofluoric acid. Both acids are contained in the composition of the electropolishing solution. They found that the stains were only formed with the solution of hydrofluoric acid – the suspected cause of the stain.
So they conducted an elemental analysis using X-ray fluorescence, the method widely used for the investigation of metals, glass, ceramics or building materials. They detected fluorine and oxygen in the stain, which indicated that the stain is an oxide film containing fluorine. The next step was to determine where the oxygen came from. First they suspected that oxygen in the air was responsible and conducted experiments in a zero-percent oxygen environment purged with nitrogen, but stains still formed.
They then tested the cavities’ moisture, suspecting that oxygen comes from water, and – bingo! – the crisp stains were formed. With more detailed investigations, scientists found that the causes of the stain are moisture and vaporised hydrogen-fluoride from diluted electropolishing solution after rinsing. The hydrogen-fluoride vaporised when diluted, and they found that it vaporised in the very low-concentration electropolishing solution.
Based on these findings, scientists conducted a test with a single-cell cavity, and succeeded in preventing the stain from forming. They will soon conduct experiments with nine-cell cavities to better their understanding of stain formation.
“We are not sure if the stain really causes the performance limit,” said Sawabe. “But now we know how to deal with them.”
Recent Comments