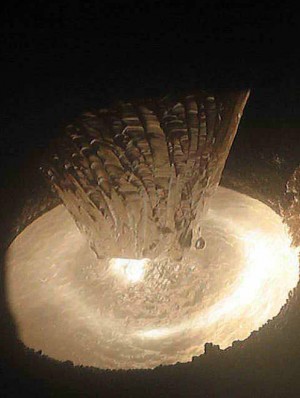
Impure niobium feedstock is being melted by high-power electron beams. The molten niobium drops into a crucible. This is one of the many steps involved in removing impurities from the metal. Image: Waldemar Singer
A significant fraction of ILC R&D has focused on the production of accelerating cavities, which requires a thorough understanding of the behaviour and properties of niobium, the metal of choice for ILC cavities.
The 2007 ILC Reference Design Report showed that the better part of the construction project effort will be taken up by comparatively low-technology standard accelerator components and civil construction. The remaining roughly 40 percent of the effort is to be devoted to advanced-technology linac parts, especially the cryogenic linac and its central component, the pure niobium sheet metal cavities. The Global Design Effort’s upcoming Technical Design Report will include one or more models of how the project would be commissioned and built.
Both ILC researchers and industrial companies have invested a prodigious amount of time and energy in understanding niobium from its extraction at the mine to its formation into accelerating cavities to the cavity’s vertical dewar qualification test. In its multiple-step treatment, niobium is reduced, purified, rolled, formed, welded and chemically polished. Most of these steps are done by our industrial partners; they have the specialised equipment and have proven their expertise during the ongoing Technical Design Phase (TDP) of ILC R&D. The final step of testing and qualifying cavity performance is best done by an institutional partner.
Niobium, found in nature as niobium pentoxide, is one of the five refractory metal elements, so named for their resistance to wear and their very high melting point. Very high-temperature reduction and purification processes are required to prepare it for our use. It must be free of low-mass gasses to less than roughly 30 parts per million.
The extreme chemical resistance of niobium makes it difficult to layer or to combine with common metals such as copper and aluminium (as done in the past at the Large Electron-Positron Collider at CERN) and still get the excellent cavity performance of 35 megavolts per metre. Typically these metals are not at all used as part of the ILC cavity production as it is impractical to keep the strong acid from touching them.
After removing gas and light element impurities, the forged niobium bar must be rolled into sheets and etched and ground to make what is referred to as a semi-finished product.
It is well known that the superconductivity of niobium is better when the residual resistance ratio (RRR) is high; a typical RRR for ILC prototype cavities is around 300. However, high-RRR material is so pure it lacks strength and the inherent fine-grained crystalline structure that is often seen in metals alloyed with various impurities. During the sheet rolling and deep-drawing process that shapes the sheets into cup-shaped half-cells, the highly ductile ultra-pure niobium can flow too much and can easily ‘cold-weld’ or stick to itself. These effects have been largely overcome in the last 20 years and with great care we can now keep voids and contaminants from being introduced at this stage. To maintain the quality of the input feedstock during this semi-finished product stage, a relatively large fraction of the feedstock, sometimes approaching 50 percent, is discarded.
The final step in cavity fabrication is the assembly of the formed, machined parts into a unit using electron beam welding (EBW). Simpler welding technology has been tried and found to be ineffective, especially for the demanding equator welds that are used to close each of the nine cells in the cavity. EBW is an automated, batch-oriented process that takes place in high vacuum. High vacuum keeps the niobium free of impurities.
Early in the Technical Design Phase the experienced DESY / TESLA team in Germany showed a cost breakdown of cavity fabrication that clearly identified EBW as a cost driver (see slide 17).
With a determined effort, the team developed a plan for an optimised set of EBW machines and associated tooling, thereby reducing production costs by a substantial factor. To prove this optimisation and to better understand the EBW process, KEK recently constructed and is now commissioning a ‘pilot plant’ cavity fabrication facility. The plant includes the forming, trimming, weld-prep etching and welding machines in a well-organised cleanroom environment. Even with delayed delivery due to the great 2011 Tohoku earthquake, we expect preliminary results during the current TDP.
The mass production models in preparation for the TDR were the central topic for discussion at the 2nd Workshop on SCRF Cavity Technology and Industrialization for the ILC. The models to be considered must balance technical considerations, such as those listed above, against the production process itself, component interface definitions, vendor models – often based on existing companies – and ILC project member in-kind contribution models. For the TDP, we can be pleased with our technical progress in understanding niobium cavity performance and with our practical progress in assembling a global industrial team for the task of building the ILC.
Recent Comments