One of the most important goals of the Global Design Effort has been to demonstrate that high-gradient cavities can be reliably produced in industry. We established two gradient goals: to produce cavities qualified at 35 Megavolts per metre (MV/m) in vertical tests and to demonstrate that an average gradient of 31.5 MV/m is achievable for ILC cryomodules. Furthermore, we set a goal of producing these high-gradient cavities in industry with 50% yield by 2010 and 90% yield by the end of 2012. We have recently achieved these ambitious goals!
The ILC reference design layout was based on an average operational gradient of 31.5 MV/m, although at that time we had not demonstrated the reality of achieving this average gradient. Our confidence came from limited R&D laboratory experiments. We then undertook a worldwide programme to qualify industrial vendors, standardise our procedures, create an integrated database and analysis, and develop techniques for identifying problems in produced cavities and fix them. (See ILC NewsLine cavity archive.)
We initiated a globally consistent up-to-date database for recording test results from different laboratories and made standard and clear definitions of achieved gradients for first-pass and second-pass yields. Rules for cavity selection were also established. We created an ILC Global Cavity Database Team that included members from Fermilab, DESY, JLab, Cornell and KEK, to carry out the analysis, present and update results so that progress of cavity R&D could be tracked. At present, the database contains information on 133 cavities, including cavities produced purely for ILC gradient R&D and others produced for other accelerator R&D.
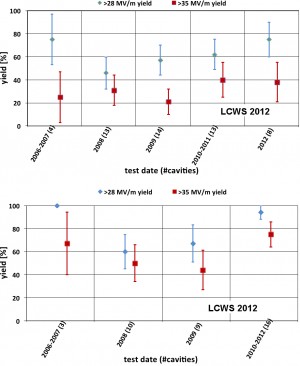
The most recent data for first-pass (top) and second-pass (bottom) yield results. Yield is the fraction of produced cavities exceeding 28 MV/m (lower cutoff) and 35 MV/m (goal). The most recent second-pass yield beyond our 28-MV/m cutoff is greater than our 90% goal.
The plots show cavities from qualified vendors that were processed according to the baseline processing cycle, which includes electropolishing. The first-pass test results drive the second-pass re-processing. If gradient exceeds or equals 35 MV/m and the quality factor Q0 exceeds or equals 8×109, the cavity is accepted; if not, the cavity is given a second-pass re-processing. The choice of second-pass process is made by the test laboratory based on first-pass test results, but a standard second-pass processes (high pressure rinse, 120°C baking, or a second standard electropolishing cycle) must be used.
The improvements are primarily due to improved diagnostic tools developed through our R&D programme that better direct the second-pass process. Incorporating second-pass re-treatment or re-processing will bring significant cost savings compared to the “over production” model used in the RDR. The technical design baseline accepts cavities with a ± 20% spread (for example more than 28 MV/m) and for our set of cavities the average gradient of the sample that exceeded that limit is actually 36.8 MV/m, somewhat higher than our 35 MV/m goal. Thus, though the statistics are limited, the two-pass standard processing has met our goals!
It is worth pointing out that there is promise of cost-effectively going beyond the yields reported above. We are developing two repair techniques that promise to improve cavity yields. The first technique involves localised grinding, a technique implemented at KEK, based on finding defects in a cavity by optical inspection and subsequently removing the defects with a miniature grinding tool. A second technique, being developed at Fermilab, uses a week-long cycle, where up to four cavities can be tumbled in parallel using progressively finer abrasive until at the end a mirror-like finish is achieved. As part of the tumbling process, light electropolishing is performed. Both techniques have already been shown to improve cavity performance.
In conclusion: we have achieved the goal of producing SCRF cavities with good yield in industry that perform at or beyond our established baseline gradient. The production process includes a standard second pass for the cavities that fail the first pass. Further, encouraging new techniques that could yield cost-effective ways are being developed to further improve cavity yields. These results establish the practicality of producing cost-effective high-gradient cavities in industry for an ILC project.
Recent Comments