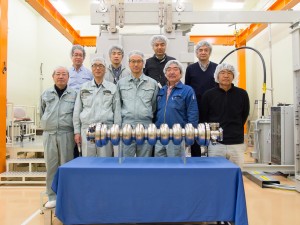
Scientists at KEK’s CFF celebrating the completion of the superconducting cavity KEK-001 Image: Nobuko Kobayashi
Sixteen thousand – that’s the number of the superconducting radiofrequency (SCRF) accelerating cavities needed to build the 500-Giga-electronvolt linear collider. The fabrications of these 16 000 cavities will be divided between the three regions of Europe, the Americas, and Asia. This week, encouraging news about SCRF cavity fabrication came form Asia.
“This is our first in-house SCRF cavity,” said Takayuki Saeki, SCRF specialist at the KEK laboratory in Japan. KEK has been working on a study for industrialisation of the SCRF cavity at a facility called CFF (Cavity Fabrication Facility) established in 2011. CFF is equipped with a press machine, vertical lathe, electron-beam welding machine, chemical treatment room, and surface inspection machine, where most of the cavity fabrication processes are done in a one-stop shop. At CFF, scientists are aiming for a high performance and high yield rate, for reducing the fabrication cost, establishing mass-production processes, and preparing the fixtures needed.
Prior to the first cavity called KEK-001, they produced a test cavity, KEK-000. “The aim of the KEK-000 was basically to gain experience with cavity fabrication, and learn the basics. This time, we focused more on mass-production,” said Saeki.
“We used the different technique to weld the equatorial part of the cavity cells for the KEK-001. We chose the technique best suitable for mass production aiming for cost reduction,” said Saeki. Scientists also adopted a cost-effective fabrication technique for the cavity end parts, which have complicated structures with components such as beam pipe, higher order mode RF coupler, power port, flanges. “We thoroughly investigate the all welding locations to determine the desirable parameters, using niobium plates and pipes. I think it worked very well.” The performance test on KEK-001 will be conducted in a few months.
Another good news from KEK is the success in the vertical test of a single cell cavity made out of large-grain niobium, which reached the record accelerating gradient of 45 Megavolts per metre. Several major laboratories have investigated the use of large-grain and single-crystal material in the past years. Large-grain and single-crystal niobium is an alternative material to poly-crystalline, or fine-grain niobium for superconducting cavities, that has potential advantages such as reduced costs and better reproducibility in performance.
Last year, a 9-cell niobium SCRF cavity made of large-grain niobium achieved an accelerating gradient of 32.6 MV/m at Peking University (PKU), Beijing, China, in cooperation with KEK. The fabrication of the cavity was finished with careful control of machining, better field flatness tuning, improved surface treatment and electron beam welding.The multiple surface treatment and performance tests on this cavity were carried out by KEK. This cavity, called PKU4, is the first cavity which has reached the requirement for the ILC both in accelerating gradient and intrinsic quality factor in China.
There are more advancements on SCRF technology in China. The Institute of High Energy Physics (IHEP), Beijing, is progressing the system assembly of the cryomodule, composed of composed of a 9-cell cavity housed in a cryostat, which maintains the cavity to very low temperature to realise superconductivity. It is now getting ready for the cold performance test later this year. This system will be a prototype to demonstrate full functioning for the ILC SCRF system requirement.
These activities and progresses indicate that China has the capability to manufacture superconducting cavities and the SCRF system integration for the ILC. “International collaboration is the key for the success for the ILC construction. And PKU4’s success is a very important milestone for superconducting technology development in China, and also for the China-Japan collaboration,” said Akira Yamamoto, regional director for Asia at the Linear Collider Collaboration. Asia is getting ready for the ILC construction.
Recent Comments