When the Pre-Lab phase kicks off with the beginning of next year, there’ll be an enormous increase of ILC R&D activities around the world. One of these is a project called “Cryomodule Global Transfer” – though “a global logistics ballet of accelerator parts” would be just as fitting. Over a period of four years, six fully functioning cryomodules (12-metre units housing the actual accelerating parts of the future 20-kilometre ILC) will be produced including all necessary components; two in each region of the ILC. That means 16 cavities, tuners and couplers and two cold-mass and vacuum vessels for each region, plus assembly and other parts.
Once the complete modules are tested in Europe and the Americas, they will be shipped to Japan, tested again, and shipped back. “This is a crucial dry run for the logistics of future cryomodule serial production and the conformity to Japanese safety regulations,” says Shinichiro Michizono, who leads the ILC accelerator design efforts in the International Development Team.
While it has become quite normal for large accelerator systems to be built in different labs and companies and shipped to the host lab, the logistic effort needed for the ILC will surpass everything that has happened before. The sooner any hurdles or bottlenecks are identified, the better, so that eventually all 8000 cavities in all 900 cryomodules that will be needed, can be installed and geared up for acceleration in the ILC main linacs.
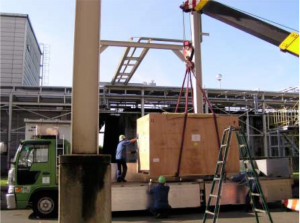
A klystron produced in Japan for the European XFEL arriving in Germany. Transporting high-tech equipment around the world complicated business and needs testing – just like the parts themselves. Image: DESY / European XFEL / KEK
The general assumption is that once the project is approved and MOUs and agreements have been signed, all regions will contribute a certain number of cryomodules to the real ILC. This saves time, as production and testing can go ahead at three different regions in parallel. However, it also means that the bulky yet high-tech accelerator modules will have to travel to Japan by ship. Recently the world had to learn that ships can get stuck in the Suez Canal… something that is hard to risk-assess. However, there are much more fundamental risks to be considered. For example, the baseline ILC cryomodule is 12.4 metres long – slightly too long for a standard 40-ft shipping container. “We are pursuing containers longer than the standard one,” Michizono explains. But if that does not work out or proves too expensive, they might have to go back to the drawing board: “If it’s necessary we will need to update the cryomodule design,” he says.
Several accelerators operating with the chosen ILC technology superconducting RF are under construction or in operation in different labs around the world, notably the European XFEL in Germany and LCLS II in the US. This means the expertise to build functioning accelerators – cavities, cold mass, tanks, tuners, couplers, you name it – exists both in industry and in the associated labs.
By the beginning of the Pre-Lab phase it will be clear which labs will lead the effort in their respective region to build the two complete modules. However, cavity production will have to adhere to the very strict “High-Pressure Gas Safety Regulations” in place in Japan for any compressed gas greater than a certain pressure or for liquified gas. Most likely the fabrication process itself and the high-pressure gas safety must be checked by licensed authorities or inspectors before cavities can be imported; if they don’t meet the regulations, the cryomodules may not be cooled down and RF-tested in Japan. The collaborators on the Cryomodule Global Transfer are prepared to do just that in case there is not enough times to produce fully facilitating cryomodules – efforts to adapt cryomodules to the Safety Regulations and the Global Transfer project would then run in parallel for simple physical shipment as the first step and for preparing the fully facilitating cryomodule shipment as the second step.
The project is expected to last the whole of the Pre-Lab phase (assuming budgets allow for it). The production of 9-cell cavities and other parts will last around two years. The fully facilitating cryomodule assembly and testing is likely to take another year. The shipping test is penciled in for year four. We’ll keep you updated on progress and further plans, hurdles and successes.
Recent Comments