Researchers in the US may soon be pumping their cavities into shape.
Last year Fermilab scientists put out a call to industrial companies to propose a procedure for hydroforming ILC-type cavities. They hope that by next year, the selected company will provide Fermilab with three hydroformed nine-cell cavities for testing.
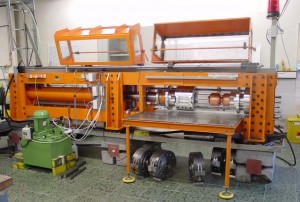
DESY’s hydroforming machine. Before being placed in the machine, a 150-mm-diameter tube is, at prescribed points along its length, ‘necked’, or spun, to a diameter of 78 mm. This forms the irises, or narrow parts, of the cavity. The necked tube is then placed in the hydroforming machine, and water in the tube presses against the metal. As a result, the tube between the irises swells to a diameter of 208 mm. Image courtesy of Waldemar Singer.
“Hydroforming’s a good idea whose time has come,” said Fermilab scientist Andy Hocker, who has led the lab’s effort in hydroforming research.
To hydroform ILC cavities, a seamless tube of niobium with the right mechanical properties is set in a cavity-shaped die. Water, pressurised to hundreds of atmospheres, is pumped into the tube and pushes out against the tube wall until it conforms to the mould. In ten minutes, the metal is shaped into the cavity’s familiar beads-on-a-string form.
The resulting shape, sculpted from a single piece of metal, is without seams or welds. Scientists see this as the method’s primary advantage over the standard procedure for forming cavities. There, 18 cup-shaped half-cells are each welded by an electron beam to the next, forming the nine-cell structure.
“The weld is such a trouble spot,” Hocker said. Welding is a complicated process, each step of which invites error. Also, most of the consequential defects in the cavity appear near welds (especially those at the equator, the widest part of the cell). “They’re a headache. Everybody would love to be rid of them.”
Being rid of them could also mean potential cost savings in fabrication and improved reproducibility in performance.
The process of hydroforming cavities from niobium tubing has been extensively researched at DESY. Waldemar Singer has led this effort within the Coordinated Accelerator Research in Europe programme. Kenji Saito has led similar R&D at KEK in Japan. Both laboratories have successfully fabricated multi-cell cavities with their developed-in-house hydroforming machines. The DESY effort, in particular, is at a stage where industrialisation is the next logical step.
But until recently, US laboratories made no notable strides towards building their own facility. Scientists at Jefferson Lab were among those who saw promise in the method.
“I’ve become quite interested in seamless cavities because their performance is good,” said Jefferson Lab’s Peter Kneisel, who is gathering additional statistics on the process by testing multiple hydroformed cavities.
Two years ago, Kneisel tested three 3-cell hydroformed cavities fabricated at DESY. The results were favorable – each yielded a gradient of about 32 megavolts per metre (MV/m).
The three have since been welded together at DESY to form a single nine-cell cavity (these welds are at the irises, which are far less troublesome than those at the equators). Kneisel is currently testing its performance at various points in the ILC baseline cavity-treatment process.
Having undergone an initial buffered chemical polish, it has already achieved 26 MV/m with no quench. Another two-cell hydroformed cavity from DESY achieved 36 MV/m after the same polish. Kneisel has another batch of three 2-cell cavities, also from DESY, waiting in the wings to be tested over the coming months.
A company in Jefferson Lab’s backyard also contributed to the US hydroforming effort. With the support of a Small Business Innovative Research grant, Black Labs in Virginia worked to produce a seamless, uniformly pliable and smooth niobium tube.
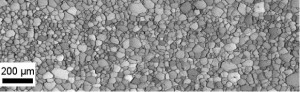
Grain structure of a Black Labs/ATI Wah Chang fine-grain niobium tube. The average grain size is 20 micrometres. The image was obtained in a scanning electron microscope. Image courtesy of Roy Crooks.
“The key to designing a tube for hydroforming was to have a very fine grain size,” said Roy Crooks, metallurgist at Black Labs. Crooks had already worked developing highly formable, fine-grain metallic materials for aerospace applications. He learned from DESY’s Waldemar Singer and others that one of the biggest nuisances for hydroforming was the metal’s coarse grain size.
Coarse grain size implies an alignment of metallic crystals. Alignment may sound like a happy trait, but a metal’s ductility is more uniform if its crystals are oriented randomly. The finer the grain size, the more likely its crystals will lie in all different directions.
Black Labs worked with ATI Wah Chang, an Oregon-based niobium manufacturer, to produce fine-grain niobium tubes. The recipe involved deforming the metal at the right temperature, which caused new crystals to be born, resulting in many fine-grain crystals that crowd out larger-grain ones. The resulting grain size was 20 micrometres, much smaller than the 200-micrometre grains of tubes tested in earlier experiments.
The metal was also significantly smoother.
“The internal surface was more like a polished piece of furniture, rather than an orange peel,” Crooks said.
In 2009 Crooks and Hocker visited DESY. Together with Singer’s team, they hydroformed tubes produced under the Black Labs/ATI Wah Chang collaboration. The tubes were formed into several three-cell units.
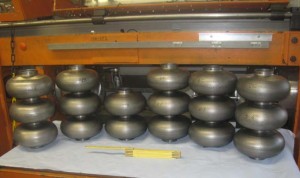
Cavities hydroformed at the DESY facility from nioboium tubes developed by ATI Wah Chang and Black Labs. Personnel from Black Labs, DESY and Fermilab formed the cavities. They received final assembly at Jefferson Lab and are currently being tested there. Image courtesy of Waldemar Singer.
The cavities have since shipped to Jefferson Lab and, along with the aforementioned DESY-fabricated cavities, will be subjected to the usual spate of tests.
One of the three-cell products achieved a 21 MV/m gradient.
“That was an encouraging result for the first cavity made from a tube developed by American industry,” Kneisel said.
Now, with Fermilab’s industry bids soon coming to a close, US labs may be able to multiply the production of hydroformed cavities.
“One of our goals is to industrialise what DESY has established, and to find out whether it can be cost-effective or at least competitive with current cavity fabrication techniques,” Hocker said. “We hope it will give us a path to achieving high gradient with high yield.”
Scientists expect that it will.
“I’ve been working in this field for 40-plus years and I’ve had my disappointments and my fun,” Kneisel said. “This work is something I believe we should really put more effort into.”
Read about the challenges of niobium materials.
I was very interested in reading of the present interest and status of Hydroforming Nb cavities. I refer to a paper from 1987 published in “Proceedings of The Third Workshop on RF Superconductivity, Argonne National Laboratory, Illinois, USA”, page 533, an invited paper:”FORMING AND WELDING OF NIOBIUM FOR SUPERCONDUCTING CAVITIES”, by Joseph L. Kirchgessner, Laboratory of Nuclear Studies, Cornell University, Ithaca. New York 14853. Both single and multicell S-Band cavities were made in Nb. Peter Kneisel performed cold RF tests on these cavities at that time. At that time the effort was limited by the availability of fine, uniform grain Nb tubing. As I sit here in my home, on the bookshelf is a 2 cell hydroformed Nb S-band cavity that was mounted on a plaque and given to me at the time of my retirement in 1997.