To realise the International Linear Collider, scientists need to address many issues. One of the most important is the primary cost driver for the ILC, the superconducting radiofrequency (SCRF) cavity and cryomodule systems. At KEK, the team responsible for SCRF activity intends to seek cost-effective mass-production scenarios for the SCRF cavity.
The ILC will have 16,000 superconducting RF cavities installed in 2,000 cryomodules. The cavities are made of pure niobium, a precious rare metal. ILC scientists are looking at a target yield of 90 percent for the cavities by working together with industrial manufacturers. As a part of this activity, KEK has set up the Cavity Fabrication Facility, or CFF, where the whole process for fabricating a cavity can be accomplished under one roof. At the end of February, scientists and engineers finished work on cavity “number zero” at CFF.
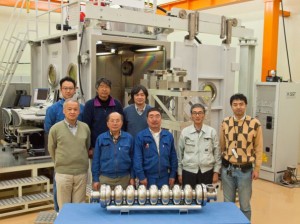
KEK researchers stand behind cavity zero, most of which was processed in the laboratory's Cavity Fabrication Facility. Image: Nobuko Kobayashi
“We built the CFF based on the world’s experiences,” said Takayuki Saeki, associate professor at KEK. “We consulted numerous research papers published by scientists at DESY, and visited DESY and RI, a German cavity manufacturer. We also visited Jefferson Lab, Cornell University, and the US manufacturer AES to collect useful information.”
DESY has already accumulated experience in manufacturing cavities in collaboration with industry for FLASH (Free-Electron Laser in Hamburg), the world’s first X-ray free-electron laser available for photon science research. The US also continues to advance its capability for industrialising cavity production. “Asia lagged behind in this area. CFF is a facility that not only helps us keep up with other countries, but also addresses the issue from a different viewpoint,” said Saeki.
CFF is a one-stop shopping facility for fabricating superconducting RF cavities. It is equipped with machines needed to make cavities: a press machine, a vertical turning machine, a niobium surface inspection device, a chemical polishing room, and an electron beam welding (EBW) machine – all in one clean environment. KEK also has an electropolishing facility for cavity inner processing and a vertical test stand for cavity performance assessments. These facilities provide a unique and valuable opportunity: a full sequence of R&D for cavity fabrication on one laboratory’s premises. “It is very important to conduct the complete process under very clean conditions, since the impurities on the material can limit its performance,” said Saeki. Once the niobium plates or pipes are carried into the CFF, they come out as cavities, without ever leaving the building in between.
Currently, scientists are trying to define the beam parameter set of the EBW machine, including voltage, current, and focus, to weld the niobium-made cavity parts. “Our goal is to establish the beam parameter set and provide it to industry,” said Saeki. “It will be effective and cost-saving for both laboratory and industry if KEK provides such parameters.” When a company establishes the beam parameters that work well for welding the cavity parts, they will be kept as an industrial secret, which is understandable. If the laboratory provides such information publicly, it can save time and money for R&D.
On 31 January, scientists finished the final welding of cavity number zero, and completed the inner inspection and electropolishing in February. But why number zero, rather than number one? “We do not call it CFF’s first cavity because, for this one, part of the process was done outside of CFF,” said Saeki.
“We wanted to start the cavity fabrication earlier than the machine installation for training purposes, so we used a pay-by-the-hour EBW machine to weld the centre parts of the cavity,” said Saeki. The EBW machine installed at CFF was imported from Germany last year. Because of the major earthquake that occurred on 11 March 2011, installation of the machine was delayed for a few months from the original plan. The installation was completed in October last year, and the welding of the end-group part of the cavity was done using the CFF’s EBW machine.
When researchers welded the centre part and end-group parts, they used the pay-by-the-hour machine again to weld using same beam parameters. Scientists faced a harsh reality at the very last stage of the cavity fabrication. “The cavity got a hole. We were shocked into silence,” Saeki said. He speculates that the cause of the hole was impurities adhering to the cavity surface. A piece of dust, even if small, would be turned into gas by the electron beam and could cause the burst. “Our choice was either to give up the whole cavity or fix the hole. So, we made an extensive study to fix the hole using niobium plates and applying them to the cavity.” KEK accumulated the experience and know-how for fixing the hole on the cavity, something that was not originally in their plans.
The completion of the performance test on cavity number zero is planned for the end of March. This test will assess the performance of the cavity, of course. But it can also check whether the hole-fixing method works or not. The first CFF cavity is expected to be fabricated during the Japanese fiscal year 2012.
Recent Comments