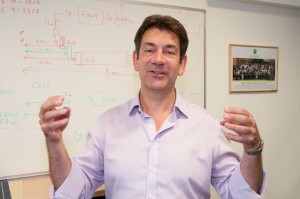
Phil Burrows re-enacting his explanation of the beam delivery system. Image: Oxford Physics Media Services
Is the beam delivery system delivering? Ten years ago, at the Global Design Effort’s formative meeting in Snowmass, Colorado, ILC communicator Perrine Royole-Degieux interviewed Phil Burrows, then professor at Queen Mary University of London, about the beam delivery system. How has the home straight where the particle bunches get squeezed, focused and brought to collision, evolved in a decade?
It has evolved a lot, says Phil Burrows, who is still working on the project, now from Oxford University. While the 2005 article still wondered whether there would be two interaction points and whether consensus would be reached for a recommendation to the ILC management, things are now much clearer. “The biggest change in the world of beam delivery was the down-sizing from two to only one interaction point,” says Burrows. The decision, taken in 2007, reduced considerably the civil engineering and beamlines and thus lowered the cost of the project. It also meant one less problem to solve for the beam delivery experts, because switching between two beam delivery tunnels while maintaining collisions and delivering high luminosity to both detectors would have been tough.
But eliminating one beam delivery tunnel didn’t mean eliminating one detector – physicists don’t back away from challenges for maximising discovery potential so easily. Instead they reinvented the interaction region, the place where electrons and positrons are actually brought to collision in the ILC. Instead of two tunnels serving two huge caverns housing one detector each, there will only be one (massive) cavern. This allows one detector to take data at the collision point while the other one is off beamline; then they swap places in an intricate detector ballet affectionately called ‘push-pull’.
After a lot of discussion, the detector, machine and machine-detector-interface teams decided on a crossing angle of 14 milliradians (mrad), “another major milestone,” says Burrows, because it meant that both selected detector concepts could adjust their designs and simulations accordingly. “But nothing is forever: we are continuing to optimise the design. At the moment we are looking at settling on the same focal length (the distance between the last focusing magnet and the actual interaction point) for both detectors, which would make machine operation easier but would also affect the inner detector design.
But beam delivery is more than tunnels and angles: beam size is critical. The beams of the ILC will need to be incredibly tiny, and the accelerator test facility ATF2 at KEK in Japan is the place where accelerator experts tweak it down to the designated beam size (in an energy-scaled version). Last year they broke the record of smallest beam size ever produced at 44 nanometres and demonstrated that they can maintain such small beams. Tests now continue to make them even smaller while increasing the beam current.
Another aspect of beam delivery is the very fast steering of the beams to make them collide at the IP, a project called Feedback on Nano-second Timescales or FONT. It is led by Phil Burrows, who says that FONT has ticked all the R&D boxes over the years: “We have demonstrated all technologies to build the intra-train beam-based feedback system. Beam position monitors with the needed resolution – tick. High-power amplifiers – tick. Prototype kickers – tick. A digital feedback system working on a bunch-by-bunch timescale – tick.” Like the others, this project continues to evolve and is already being used and adapted for other linear collider applications: the technology is used in the CLIC test facility CTF3 as a feed-forward system. “It makes sure that the drive beam, CLIC’s unique acceleration concept, will arrive at the accelerating structure at exactly the right time,” Burrows says. He should know: he became CLIC accelerator spokesman in 2014.
Recent Comments