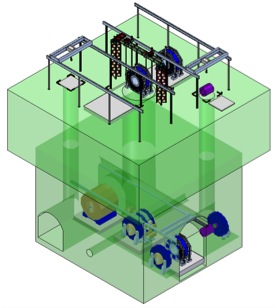
A heavy-duty crane on the surface will transport the assembled detector slices to the hall below. Graphic: Marco Oriunno
Sometimes big things have to move in the way of small things to find exciting things. The ILC detectors, for example. True to the scientific principle of reproducibility of results, two detectors, ILD and SiD, will one day record what happens when electrons and positrons collide so that one can verify (or not) what the other has observed, using different detection technologies. However, they will never be able to do this simultaneously as there will be only one interaction point. The detectors will have to move into and out of the beam in as short a time as possible for maximum data harvest, and this caused detector designers, machine experts and the guys who know all about shifting rock no end of headache. Now they have found a solution that addresses all problems (at least for an ILC that is not built in a mountainous region).
The final design for the non-mountain hall for the detectors is shaped like a Z. The downstroke, which actually is at right angles to the side bits, is where the beams come in, and the side bits are the garages for the detectors when they are not in use. Though rather compact compared to the LHC’s giant ATLAS detector, both ILD and SiD are heavyweights, and with dimensions up to 16 metres in length and up to 15,000 tonnes on the scales, they are not easily pulled around. The total surface area of the hall, therefore, also measures over 3300 square metres. This allows not only for smooth operation, but also for easier assembly and maintenance.
Assembly is the main argument for the final choice of shafts that are needed for the ILC’s collision point. There will be one big shaft, 18 metres in diameter, right above the central part of the Z for the lowering of the giant detector slices, magnet coils and endcaps. Like the CMS detector at CERN, the two ILC detectors will be assembled on the surface and then lowered underground in complete slices. Two smaller shafts – nine and ten metres in diameter – give access from above to the two garages for detector maintenance, and another two are for people only so that they can get down and up easily and also have an escape route in case of an evacuation.
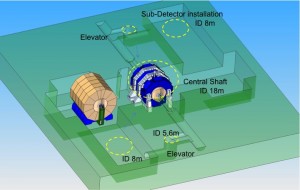
Spot the Z shape – one detector in parking position, one taking data. The non-mountainous detector hall for the ILC could look like this. Graphic: Marco Oriunno
Now obviously things will not be as easy as they may sound here. “We faced the problem of how to make both detectors fit the space between the two tunnels. And it’s the first time in history that two detectors share one interaction space in a push-pull-configuration,” says Marco Oriunno of SLAC, a member of the common task group on machine-detector interface and responsible for the impressive 3-D graphics of the area.
How do you move a 15,000-tonne object from a garage into the beam and back some 15 times a year? How do you make sure none of the high-tech, mega-precise parts move during the transport? How do you keep the magnets cool? The answer is: concrete slabs that serve as platforms for the detectors and will be moved by either airpads or rollers, and flexible cryogenic lines that move with the moving detector. A set of compressors on the surface makes sure that enough coolant is around while two cold boxes, one for each detector, will be installed underground. The lines extend from the garage to the interaction point. And the detectors adapted their configurations to each other so that both reach the beampipe shielding that sticks out at both sides of the central hall. Both also had to be self-shielding with respect to ionising radiation and magnetic fields for hall safety.
The shielding around the beampipe and the detectors’ self-shielding material are the only protective screens needed for the hall design. Maintenance on one detector will be possible underground while the other is busy taking data. The group also thought about how to organise beam commissioning. Before you start colliding particles, the machine operators have to take a series of important steps to truly understand and control their machine. A stray beam can cause great damage in a sensitive detector, so commissioning will not happen with a detector in place. Instead, walls of shielding blocks will be erected around the beam pipe so that work can continue on both the assembly of the detectors and the commissioning of the accelerator.
All this will be very different if the ILC is built under a mountain range. Shafts will not be vertical, for example, and the transport of the detector parts will be different. The design of the hall for these conditions is still a work in progress. Similarly, a civil engineering company is currently working on detailed studies of what can be expected of the non-mountainous geology when five shafts of different diameters are dug within relatively close distance to each other, and a detailed design of the moving platforms. Stay tuned for future info!
Recent Comments