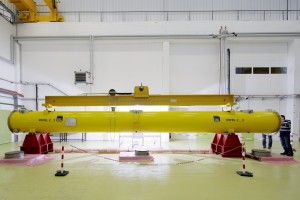
Having a good look at cryomodule production: an industrial study produced interesting results. Pictured: a cryomodule for the European XFEL under construction at CEA Saclay. Image: DESY / Heiner Müller-Elsner.
An industrial study commissioned by the Global Design Effort in collaboration with experts from CERN gives a clearer picture of how cryomodules for the ILC could be mass-produced by industry. The study, whose results were recently presented at a meeting between accelerator experts from different labs. A similar study has looked at cavity serial production. One of the scientists leading the cryomodule study, Vittorio Parma from CERN, was the driving force behind the cryostat assembly for 2000 cryomagnets for CERN’s Large Hadron Collider between 2003 and 2008 and thus predestined to lend his experience to the project.
For the ILC, cryomodules could be assembled in labs – just like those for the European XFEL are built at CEA in Saclay, France –, or in industry. A cryomodule for the ILC consists of eight cavities plus a quadrupole or of nine cavities in a string, each cavity embedded in a helium tank, plus insulation, support pipes and extractions pipes, couplers and much more. The work that needs to be done is similar in complexity to the production of the magnets and cryostats for the LHC at CERN, with cryostats for dipoles being less complex than a full cryomodule, but quadrupoles a lot more complex. As nobody has ever industrially produced a series of cryomodules (some 1800 will be needed for the ILC), the production of 100 XFEL cryomodules is an important, and almost the only, point of input.
“Originally it was planned to assemble the dipole magnet inside their cryostats at CERN and the quadrupole magnets in industry,” explains Parma. But the company went insolvent. In order to be ready for the LHC start-up in 2008, the machine experts decided to assemble everything at CERN: dipoles, quadrupoles and their cryostats. “We did a work that was typically industrial – basically we learnt how to set up a factory,” says Parma. Labour workforce was found through external contractors, while planning buildings and infrastructure, devising production procedures and studying tooling options and possibilities for automatisation became daily business. “We did it the dirty way because we had to do it within limited time, without the typical preparation phases with prototyping which normally preceeds series productions; and we hope we can help both the European XFEL and the ILC with the experiences we have made”, concludes Parma.
For the study, the ILC/CERN team worked together with the German company Babcock Noell, who they knew from previous contracts and who based their industrial study on cryomodule production for the European XFEL. Study leader from the industrial side was Christian Boffo. The goal was to find out the most cost-effective way of producing ILC cryomodules by studying the assembly phases and the production lines and factory layouts required in order to produce the about 1800 cryomodules with the required quality and within a time frame of about four to five years. “You would need enormous facilities of up to 40 000 square metres surface area that will have to be built and planned from scratch,” predicts Parma. These facilities would house a number of cleanrooms of unprecedented size, with a few hundred people in the facilities at any time.
The goal of the study was also to look at possible processes that can be automated to save time and labour cost. But there are also assembly steps that can only be done by humans. “We have to tell industry the competency limits of both machines and of workers,” explains Parma. “Can the couplers be inserted by a robot? Probably not. Can the string of cavities in the cleanroom be aligned by a robot? Possibly – there is a proposal for an alignment table. But we may need some type of validation for that. We also touched orbital welding of the cavities, but the cleanliness of a class-10 cleanroom make this option unacceptable with the technologies available and would require a considerable redesign effort. This is all stuff the industry needs to hear from us.”
By the way: there is another possibility for an automated process that could reduce the time spent on this particular part of the assembly process: leak-checking of welds on cryomodule piping by using the so-called clam-shell method, as proposed and patented by CERN. Considering the time saving and reliability of this technique; the European XFEL could be adopting it soon during the assembly of their cryomodules at CEA Saclay.
The study looked at two possible scenarios: 100% production by a single company and 30% production by three different companies. The latter is not an unlikely model because the cryomodules for the ILC could be produced in the three different regions by different vendors, rather than by just one vendor from one region. The study showed that the 30-percent model would indeed need one third of the infrastructure and staff. “This 30-percent option indeed seems more reasonable,” concludes Parma. Size and infrastructure of the individual facilities around the world would be easier to handle, and could be exploited for future use by the hub laboratory where the facilities would be set up.
After eight months of intense study and several meetings and visits, the company passed on their conclusions in October. After reviewing these, the ILC/CERN team has worked out their own conclusions. “I would say that the study has provided a solid and valuable input for the ILC cost estimate,” resumes GDE Project Manager Nick Walker from DESY. “This study (like those that preceded it) demonstrate that this level of production is quite feasible. Although the facility is quite large, it is not unreasonable. Industry is quite capable of gearing such facilities up.”
Recent Comments